CEMENT
Limestone Mining
Limestone is the major component of cement. Since the limestone from the quarry is variable, one needs to load from different areas in the quarry to ensure that the limestone quality is more consistent. Knowing what quality is currently on the pile then dictates from which areas in the quarry must be loaded from.
Limestone Quarry Life of Mine can be extended by using Minalyser to guide limestone mining processes. This prevents mining prematurely depleting high grade limestone ore and reducing the lifetime of the mine.
Raw Mill
Small quantities of Fe, Al and Si, are added to the limestone clay mixture before the raw mill. Minalyser not only ensures that the blend ratios are at an optimum, but it also simultaneously monitor contaminant levels for excessive concentrations of sulphur, magnesium oxide, sodium and potassium.
To monitor Raw Mill efficiency, a Sympatec Mytos PSD Analyser can be installed.
Kiln
Kiln consistency is critical to successful clinker production. The fuel properties and the burner settings control the shape of the flame. A too long or too short flame impacts negatively on the burning conditions. If for instance the ash content of the fuel is high, the flame length will increase. Then the burner settings and kiln operation must be adopted to shorten the flame back to its desired shape. If the fuel ash is however variable, it will cause unstable operation as the flame shape will change continuously – the clinker quality will therefore be variable as the corrective actions cannot change the operation that fast. Therefore, the properties of the coal to the kiln must be as consistent as possible.
Minalyser’s ability to measure organic and inorganic material mean that the Calorific and Ash values can be monitored and optimised by blending and stockpiling coal prior to the coal mill. Particle size of coal fed to the kiln can also be controlled with installation of an PSD analyser after the Coal mill.
Cement Mill
The SO3 level in cement impact on the setting time and strength development of the cement. Tighter control of the SO3 level will therefore produce a more consistent cement. This can only be achieved in real time with online measurement of the Cement Mill Feed.
Downstream of the Cement Mill the product fineness is measured continuously and changes to the process can be made faster to ensure product stability. and after coal mill. The product residues are monitored on a continuous basis by manual sampling and screening, or benchtop PSA. Operators then tend to operate the mills with relatively fixed settings. Particle Size Measurement after the cement mill ensures product consistency and stability
ScanMin Minalyser typically report
• Manganese as % Mn2O3
• Titanium oxide as % TiO2
• LSF Ratio (Lime Saturation Factor)
• SM Ratio (Al2O3% / SiO2%)
• AM Ratio (Al2O3% / Mg2O%)
Most GADRA analysers only measure free moisture by using microwave technology. MINALYSER measures Oxygen and Total moisture. MINALYSER can differentiate between:
– Total O
– o in moisture
– o in oxides
– Organic oxygen
MINALYSER also measures H, combined with a microwave moisture monitor it will supply Total. Inherent and free moistures values.
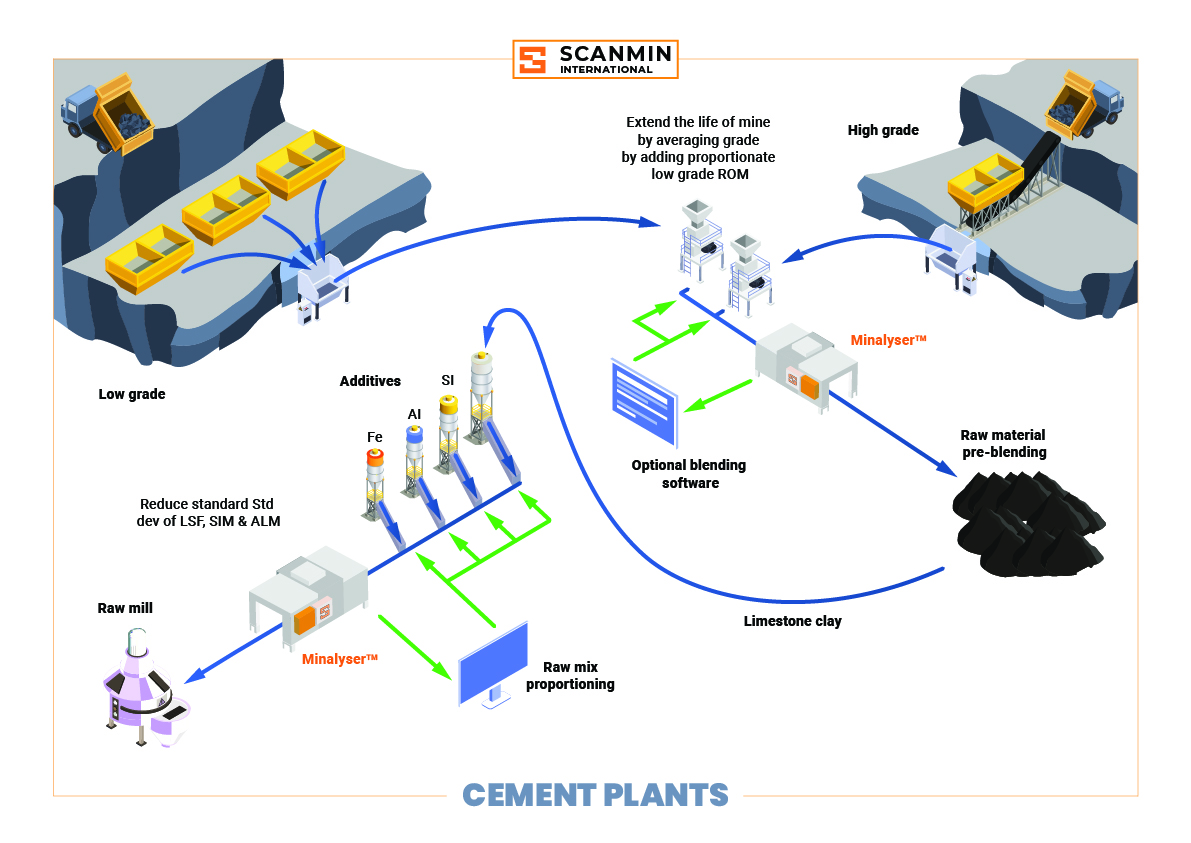